There are two key reasons for improving warehouse efficiency; customer satisfaction and the bottom-line.
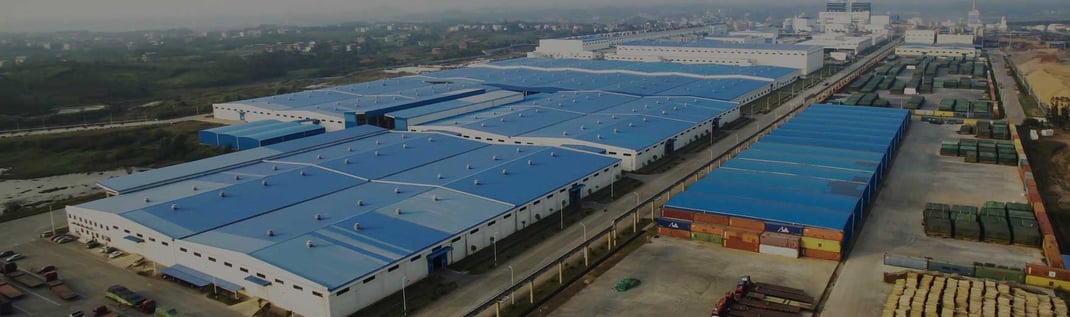
Put simply, an efficient warehouse is able to fulfil orders quicker and more accurately which leads to happier customers. But great warehouse efficiency is more than just making sure the right goods are in the right place at the right time, it’s about saving time and money by optimising productivity.
And technology is now firmly in the driving seat for taking warehouse efficiency forwards. From connected clothes and smart glasses to workforce management solutions and 3D sensors, technology is empowering rapid and revolutionary changes within the warehousing industry.
Chief among these is workforce management software, like Quinyx, which can integrate with traditional warehouse management systems, making the workforce as efficient as the warehouse itself.
It’s a simple solution for improving warehouse efficiency, here’s why:
It saves time on admin. We know warehouse managers are happiest when they are managing a warehouse, not when they are stuck in front of a computer screen managing rotas. A WFM solution will automate core processes like scheduling saving a manger, on average, 9 hours per week. This time can then be re-invested into optimising the way the warehouse operates.
It makes life simple for employees. Not only does it benefit managers, it’s great for employees. Quinyx comes complete with a mobile app so employees can see when they are working, swap shifts and make requests for additional shifts all through their phone. This leads to employees who are more engaged and happier at work. As well as bringing a natural boost to their individual productivity, this also has a positive impact on staff retention levels.
It keeps quality high. High standards are everything in an efficient warehouse. By using a workforce management solution, warehouse managers are able to access real-time insights into who is doing what job and when they are doing it. This level control allows to ensure standards always remain high.
It controls labour cost. Labour is traditionally the most difficult cost to control for a warehouse manager and forms a high percentage of the overheads. Even single-digit percentage savings can translate to a huge impact on the bottom-line. Systems like Quinyx will give instant feedback on hours scheduled and worked against hours budgeted and forecast for. If certain operations are always running over budget you’ll be able to see where they are and implement any necessary changes to control the cost.
It makes forecasting easy. There’s nothing worse than being hit by the unexpected. Whether it’s Black Friday sales or the launch of a new product, being able to forecast times of peak demand, and what exactly that demand will be, can hugely improve your efficiency. By connecting Quinyx’ forecasting module to the system that monitors incoming and outgoing packages, you can actually staff more accurately based on metrics for your own systems.
We have seen this in action with Yilport who forecast staffing based on the size of the ship coming into port. For example, a vessel ‘type 5’ means they need to schedule 7 crane drivers, 5 trucks drivers and so on.
Join us for a free webinar with Peter Ward, CEO of the UK Warehouse Association, on Wednesday, June 28 to find out more about how warehouses are using technology to improve efficiency and combat the challenges they face.